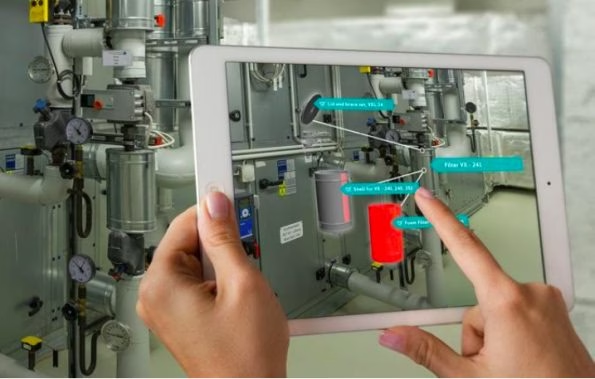
How Applying AI in Manufacturing Will Save Billions of Dollars for Industry?
In this blog post, aimed at those interested in artificial intelligence and manufacturing, we turn our attention to how artificial intelligence in manufacturing will save the industry billions of dollars.
Collaborative Robots and Adaptive Manufacturing
Robots aren‘t a new idea in the manufacturing industry. Since they were introduced into production lines in manufacturing sites decades ago, suppliers have been able to satisfy increasing consumer demand for products by automating specific steps and workflows throughout the manufacturing process. Sometimes, this has resulted in the loss of specific jobs, but for the most part, these collaborative robots have augmented existing human capabilities and enhanced productivity.
The introduction of artificial intelligence to the manufacturing industry is the next evolution of this and will help manufacturers realize even more cost savings. It will also continue to enhance human capability and optimize the manufacturing process.
The world is in the middle of the 4th industrial revolution, and with artificial intelligence and automation driving this, it‘s understandable that the human workforce may feel that employment is threatened, but just like previous industrial revolutions, those who retrain and upskill will be able to adapt to this new AI-powered industry.
DHL and Locus Robotics
Consider for a minute the partnership that DHL formed with Locus Robotics, an order fulfillment robotics company, back in early 2017. Locus Robotics was able to supply DHL with robots that worked alongside their human counterparts could help them locate and pick products for shipment.
Get a complimentary discovery call and a free ballpark estimate for your project
Trusted by 100x of startups and companies like
The technology means that product selection time is reduced, as is the chance of humans making mistakes, which ultimately translates into greater efficiency and, therefore, cost savings for the courier.
Deploying a solution like this at scale, globally, can only bring vast savings for businesses in the e-commerce and order fulfillment sector.
Adaptive Manufacturing
Possibly, one of the most promising aspects of introducing artificial intelligence into the manufacturing industry will be the concept of adaptive manufacturing.
Robots often must be preprogrammed to perform tasks that are normally repetitive and follow a sequence of steps. If the robot needs to perform a new task, it must be reprogrammed, which means robot downtime, loss of productivity, and so on.
In 2012, technology and robotics firm Rethink Robotics introduced “Baxter” to the market. Baxter is a fully integrated robot solution powered by a software platform that leverages many different technologies, such as vision and sensory cameras.
All of which let the collaborative robot adapt to real-time events in the manufacturing process. You can read more about Rethink Robotics and their collaborative robot technology here if you‘re interested.
Fusing advancements in robot technology with artificial intelligence, we can see how AI brings more flexibility to the manufacturing process by letting robots learn routines from human workers, thereby removing the need for robot reprogramming and downtime, again driving cost savings for manufacturers.
Predictive Maintenance
Normally, industrial equipment is maintained on a fixed schedule, regardless of the condition of each component. This can sometimes result in wasted effort and/or undiagnosed component failures. Imagine your car could notify you that a component in the engine or electrical unit was about to become faulty, prior to the actual breakdown or malfunction of the component, and give you sufficient notice before you make your next trip.
Predii
Predii, a predictive maintenance AI company based out of Palo Alto, is one company that is helping to make this vision a reality.
The firm's solution uses a network of sensors to provide streams of binary data that log measurements, such as position, speed, temperature, and so on. From a maintenance and repair perspective, being able to log and identify discrepancies in these sorts of attributes is key to being able to predict if a component is about to fail.
Complex mathematical models are used to identify “regular” operating conditions. The system then continuously checks components, feeding data back to Predii and surfacing signals that don‘t fall within the “regular” operating threshold.
Taking this a step further, the technology that Predii is creating could potentially be integrated with manufacturers' supply-chain management procedures to help drive efficiencies in the supply-chain management process.
Predii could predict, at scale, components were about to fail, and that the manufacturer could receive a notification via devices connected to the cloud, all of which help manufacturers better plan component production and therefore ensure that stock levels are optimal. With a possibilist like this, one can see how predictive maintenance, powered by artificial intelligence, has the potential to save billions of dollars globally for manufacturers.
Finally, according to a recent report on the 4th industrial revolution we‘re currently experiencing by tech resource DZone, the market for predictive maintenance was set to grow from $2.2 billion in 2017 to $10.9 billion by 2023. That‘s a 39% increase in annual growth!
Hire expert developers for your next project
1,200 top developers
us since 2016
With forecasts like these and increased adoption of predictive maintenance solutions, manufacturers will be able to further drive cost savings by optimizing their asset and component management processes.
Augmented Reality and Employee Training
Manufacturing typically involves the construction of many components in a specific order as quickly as possible. The process is the same whether it be cars, phones, or passenger jets and regardless of the item being produced, new sets of instructions, sometimes in a BOM (Bill of Materials) need to be drafted and shared with the production line teams.
Sometimes, these manufacturing instructions can be out of date or hard to follow for manufacturers, but one company is working to change this.
Vital Enterprise
Vital Enterprise is a firm based out of Silicon Valley, California, that creates augmented reality software for human workers in manufacturing environments. The firm‘s solution, which runs on smart glasses, provides manufacturing employees with a voice-controlled, hands-free solution, and using the inbuilt screen on the smart glasses, can display all work instructions and technical drawings for each component.
The technology even lets users view associated drawings and videos from the previous person who completed the job.
Employees Training
Employees generally need to be trained in terms of knowing which procedures to follow when components roll off the manufacturing line. This can often be a time-consuming process. Augmented reality has the potential to reduce training time for new starts and save manufacturers valuable dollars.
Jaguar Land Rover (JLR), collaborated with Boch and RE‘FLEKT, who provided JLR with an augmented reality solution that gave users “X-ray vision,” which allowed trainees to see directly inside cars and identify the exact location of components.
All of this could naturally be done without having to remove or reinstall dashboards and side panels, thereby vastly reducing the time taken to train each employee.
Employees simply point an iPad with the application at the dashboard, and users can “see” everything that sits behind paneling, which includes, but is not limited to, internal wiring, sensors, connections, and so on. More importantly, connection and wiring diagrams are displayed in the application, which allows training to be performed without having to waste time reassembling components.
The blending of Innovative technologies such as augmented reality and smart glasses can only drive even more efficiencies on the manufacturing and production line, as it means that skilled workers no longer need to walk back over to a workstation to verify instructions at a workstation.
3d Printing
3d printing in its regular form contains no artificial intelligence algorithms, but in this current AI-powered revolution we‘re living in, complex algorithms can be used to suggest optimized or simplified structures as humans model designs in popular CAD tools.
As the human designer iterates their way to a solution, the designer can choose which option best fits the task at hand, taking material and structure into consideration, of course.
Ai Build
Ai Build is a firm based in London, UK, that specializes in artificial intelligence, 3D printing, robotics, and manufacturing. The firm offers a subscription-based service that gives their clients access to autonomous large-scale 3d printing technology and has a number of products that make it easy to manage the entire manufacturing lifecycle, and with their product AiSync, this can even be done over the internet!
Hire expert developers for your next project
AiSync allows manufacturers to upload designs for 3d printing (via AiBuild – another product) and then simulate the manufacturing process if they want to. Analytics are presented to users, who can then tweak and adjust the process. Being able to do this in a simulated environment has the potential to save manufacturers millions, as it is all being simulated on a computer using artificial intelligence
The firm has another product called AiMaker that integrates with AiSync, AiMaker which can be connected to existing manufacturing robots and turn them into 3d printers that can print a number of thermoplastic materials.
When AiMaker is integrated with AiSync, manufacturers have the benefits of both worlds in that they can simulate what *could” happen in the manufacturing process with newly uploaded designs as well as having a 3d printer that can take the most optimal design, make printing decisions in real-time detect anomalies and create the actual product, all powered by artificial intelligence.
Being able to simulate manufacturing workflows and reiterate designs without firing up the physical production is a game changer, especially when fused with a robotic 3d printer that can take the analytics from the most optimal simulation and has the potential to increase efficiency, reduce downtime, and costs.
Internet of Things (IoT) and Devices
The Internet of Things (IoT) and the rise of smart devices have been growing exponentially in recent years. Industry analysts predict there will be as many as 41.6 billion connected devices by 2025!
The McKinsey Global Institute of researchers believes that the impact these smart devices will have on the global economy could be as high as $6.2 trillion by 2025. Smart devices like these can be equipped with sensory and semiconductor components that allow the capture of real-time data from physical equipment and locations in manufacturing plants. The data can then be transmitted to data repositories in the cloud for further analysis by artificial intelligence systems.
From an artificial intelligence perspective, data is the oil that powers the underlying algorithms that help mimic human behavior, and accessing data from an ever-increasing IoT ecosystem, coupled with this data, has the potential to give manufacturers rich, actionable insights into the performance of production lines or robotic equipment.
With the rich datasets that IoT devices provide, manufacturers will be able to integrate real-time data signals from manufacturing sites located around the world and be better placed to make company-wide decisions more quickly.
All of which, collectively, will be able to ultimately save manufacturers time and, more importantly, revenue!
If you need expert developers skilled in AI technology to build next-level software solutions, contact DevTeamSpace via this quick form, and partner with our expert developers for your next software development project.
Frequently Asked Questions
Artificial intelligence can be used to improve just about any process that involves computers or can be controlled or monitored by software programs. Today, AI is being heavily used in finance, the medical industry, and many others.
• IBM Watson
• Google Analytics
• Deep Vision
AI will allow for far more automation as well as efficiency savings. It will speed up processes as well as ensure supply chains are not interrupted.